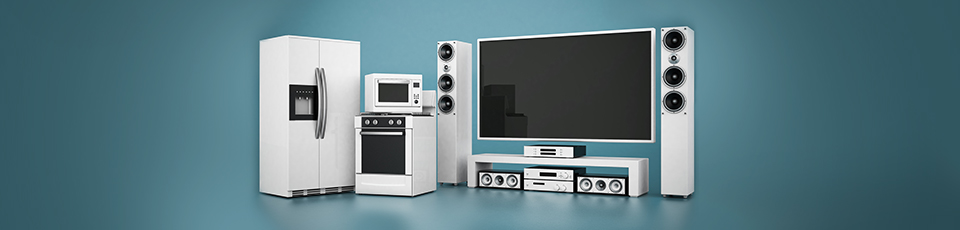
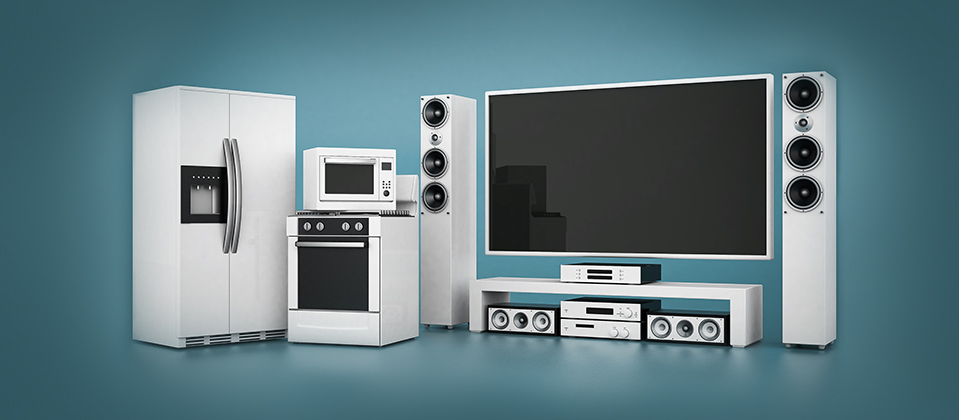
도장종류
수동 도장
에어건을 이용하여 사람이 직접 피도물에 도장 하는 방식
장점 | 작업자가 직접 육안으로 확인하면서 작업이 가능하므로 도장 시 발생하는 외관 문제에 즉각적으로 대처가 가능함 |
---|---|
단점 | 작업자가 미숙련자 인 경우 각 피도물의 작업 결과(도막 두께 및 외관 등)가 일정하지 못함 |
스핀들 라인 도장
각 피도물을 회전 컨베이어에 결합하여 스프레이 건 터널을 통과하면서 도장하는 방식 (핸드폰 부품 및 소물 도장에 주로 적용)
장점 |
|
---|---|
단점 |
|
다관절 로봇라인 도장
산업용 로봇을 활용하여 도장물에 도장하는 방식
장점 |
|
---|---|
단점 |
|
도막 결함의 원인 및 대책
구분 | 현상/원인 | 대책 |
---|---|---|
티 불량 |
|
|
크레터링 |
|
|
침식 |
|
|
도료를 통해 개선할 수 있는 방안
- 용제 사용 전에 처리를 통하여 침식을 미리 발생시키고 색도료 도장을 실시하여 침식부위를 가림.
- 프라이머를 사용하여 침식발생 부위 위에 도막을 형성한 다음 색도료 도장을 실시함.
- 속건형 신나를 사용하여 침식이 발생할 타이밍을 주지 않고 건조를 유도함.
- 플라스틱 소재에 침식이 발생하지 않은 용제를 파악하여 적정한 희석액을 제조,사용함.
(위의 방법들은 일정 부분 침식개선은 가능하나, 근본적인 해결방법이 아님을 유의하시기 바랍니다)